BGA実装のさらなる品質向上を目指し、JTAGバウンダリスキャンテストを導入いたしました
- 導入目的1未検査領域をなくす
- BGA部品の実装においては、従来設備で検査できない未検査領域を「いかにカバーするか」が弊社の課題でした。JTAGバウンダリスキャンテストの導入により、未検査領域を大幅に削減しほぼ100%の検査カバレッジを確保しました。
- 導入目的2見えない工数の削減
- 不具合発生時、弊社では不具合箇所を特定するためX線による解析を行っておりましたが、不良がオープンモードである場合、膨大な時間と工数を要しておりました。JTAGバウンダリスキャンテストの導入により、ショートモード・オープンモードに関わらず不具合箇所の特定が容易になり、解析に要する時間が大幅に短縮されました。
- 導入目的3品質保証への取組み
- JTAGバウンダリスキャンテストとICTをインライン検査として組み合わせることで高い組立品質を実現します。また各検査工程で得られたデータを上流工程にフィードバックすることで本質的な品質向上にも取り組んでおります。不具合品の再発防止・流出防止はもちろんのこと、予防対策にもしっかりと取組み、顧客満足の向上に努めてまいります。
小ロットのBGA実装では、未検査領域拡大による市場への不具合流出が懸念されており、この解決が顧客満足の向上に繋がります。
JTAGバウンダリスキャンテストを導入するまでは
BGA部品の普及に伴い、弊社においても多層基板の部品実装が多くなり、インサーキットテスタ(ICT)でのプロービング領域が必然的に減少し、その結果BGAデバイスの実装保証については、リフローの温度プロファイル管理に依存せざるを得ない状況が続いておりました。この状況を打開しようと透過型X線検査装置を導入しましたが、弊社の場合、ショートモードの不良検出には有効なものの、オープンモードの不良検出に関しては熟練した検査観察技術が必要であり、短時間で不具合箇所を特定することが難しく、BGA実装の品質向上のためには更なる取組みが必要となりました。
JTAGバウンダリスキャンテスト導入の効果
そこで新たにJTAGバウンダリスキャンテストを導入し、従来検査とのコンビネーションによりBGA実装基板の検査領域をほぼ100%とすることができました。例えば、基板外形200×180mm、256ballsと668ballsの2つのBGAデバイスを搭載した基板の場合、導入前の検査領域は約30%にとどまっておりましたが、導入後の検査領域はほぼ100%となりました。
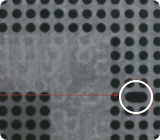
半田ショート不良は検出が容易にできる
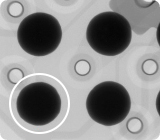
半田オープン不良は検出が難しい
[事例] 外形200×180mm・256ballsと668ballsの2つのBGAデバイスを搭載した多層基板
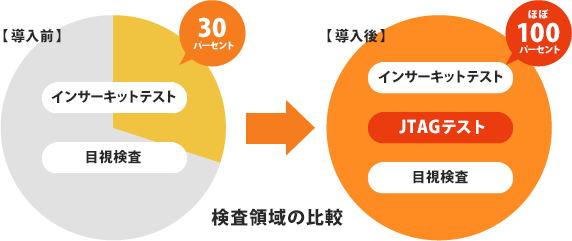
従来検査とJTAGバウンダリスキャンテストのコンビネーションで検査カバレッジ100%を目指します